Molding Plastic Injection: An In-Depth Guide
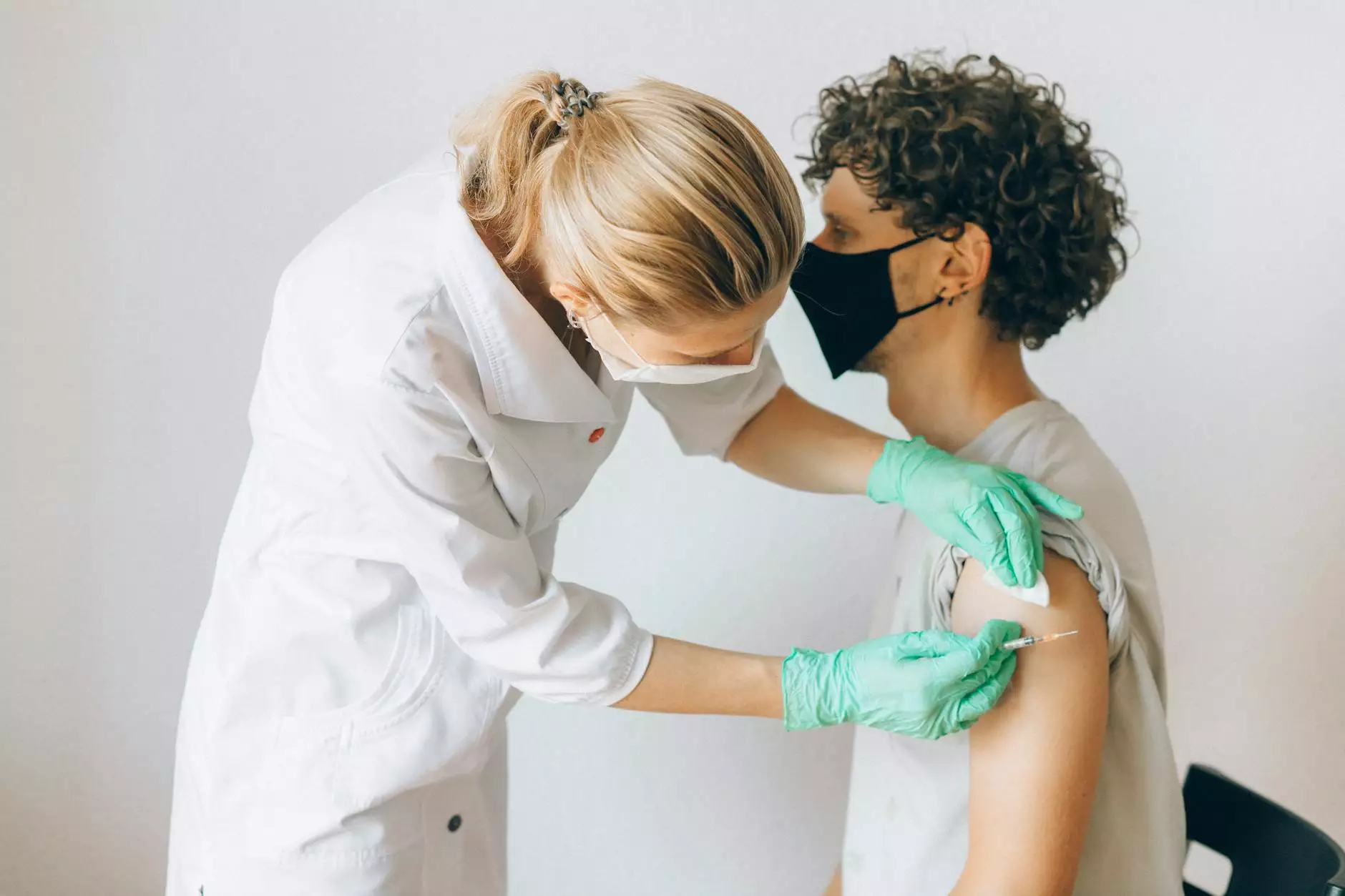
Molding plastic injection is a revolutionary process that has transformed the manufacturing and fabrication industries. This technique allows for the creation of complex shapes and designs with high precision and efficiency. In this comprehensive article, we will explore various aspects of molding plastic injection, its benefits, applications, and its pivotal role in the business landscape, especially for metal fabricators like DeepMould.net.
The Fundamentals of Molding Plastic Injection
Before delving deeper into the specifics, it's crucial to understand what molding plastic injection entails. This process involves melting plastic and injecting it into a mold where it cools and solidifies into the desired shape. The key components of this process include:
- Injection Molding Machine: This machine heats the plastic and injects it into the mold with precision.
- Injection Mold: A custom-made mold that shapes the plastic into the desired form.
- Plastic Resin: The raw material, usually in the form of pellets, that is melted and molded.
How Molding Plastic Injection Works
The process of molding plastic injection can be broken down into several key stages, each playing a vital role in the overall effectiveness of the method:
- Material Preparation: Plastic pellets are fed into the injection machine, where they are heated until they reach a molten state.
- Injection: The molten plastic is injected into the mold cavity under high pressure.
- Cooling: The injected plastic is allowed to cool and harden inside the mold.
- Demolding: Once cooled, the mold is opened, and the finished part is ejected.
- Finishing: Additional processes, such as trimming or painting, may be performed to enhance the final product.
Advantages of Molding Plastic Injection
The popularity of molding plastic injection arises from its numerous advantages, particularly for manufacturers:
Efficiency and Speed
One of the primary benefits of plastic injection molding is its high efficiency. The entire process, from heating the plastic to final product delivery, can occur rapidly, enabling high-volume production.
Precision and Detail
Injection molding allows for intricate designs and tight tolerances that are often difficult to achieve with other manufacturing processes. This level of precision makes it ideal for products requiring exact specifications.
Cost-Effectiveness
While the initial setup cost for molds can be high, the long-term savings from mass production and reduced waste make molding plastic injection an economically viable option for many businesses.
Material Versatility
This method supports a wide array of plastics, including thermoplastics and thermosets, giving manufacturers the flexibility to choose the best material for their needs.
Environmental Considerations
Modern injection molding techniques are now compatible with recyclable materials, promoting sustainability in manufacturing practices.
Common Applications of Molding Plastic Injection
Molding plastic injection is used across various industries due to its versatility:
Automotive Industry
The automotive sector employs injection molded components for everything from dashboard panels to interior trims, enhancing durability and reducing weight.
Consumer Goods
Products such as toys, electronics casings, and kitchen ware are typically manufactured using this technique due to its efficiency and precision.
Healthcare
In healthcare, molding plastic injection is used for creating components like syringes, IV bags, and various medical devices, where sterility and compliance are critical.
Packaging
Injection molded products are vital in the packaging industry, producing containers and lids that meet both safety standards and consumer demands.
Innovations in Molding Plastic Injection
As technology advances, so does the process of molding plastic injection. Innovations such as:
- 3D Printing Integration: Companies are using 3D printing for fast prototyping of molds, reducing lead times.
- Smart Manufacturing: IoT-enabled machines allow for better monitoring and efficiency during production.
- Advanced Materials: New composite materials are now available, providing greater strength and reducing weight without compromising quality.
Challenges in Molding Plastic Injection
Despite its many advantages, the molding plastic injection process does come with certain challenges:
Mold Design Complexity
Creating precise molds can be complex and require extensive engineering knowledge, often leading to high initial costs.
Material Limitations
While the versatility of materials is a strength, not all plastics can withstand the heating and cooling cycles involved in the process.
Environmental Concerns
While advancements are being made in recycling and using biodegradable plastics, traditional plastic use still raises significant environmental concerns.
The Future of Molding Plastic Injection
Looking ahead, the molding plastic injection process is poised for significant growth and change:
Emphasis on Sustainability
Companies are increasingly focusing on sustainable practices, which includes using recycled materials and energy-efficient machines.
Customization through Technology
Advancements in software and manufacturing technologies are enabling greater customization, allowing businesses to cater to specific market demands with speed and efficiency.
Global Market Trends
The global demand for molded plastic products continues to rise, driven by growing industries such as automotive, consumer electronics, and medical devices.
Conclusion: Embracing the Power of Molding Plastic Injection
In a competitive business environment, understanding and leveraging molding plastic injection can provide a significant advantage. Companies like DeepMould.net exemplify how integrating this efficient and versatile manufacturing process can lead to enhanced production capabilities and satisfied customers.
As industries evolve, businesses must remain adaptable and responsive to change, and molding plastic injection is a critical component of that strategy.
Investing in the right technologies, training, and partnerships will ensure that businesses not only survive but thrive in this dynamic landscape.