Understanding High Pressure Die Casting Tooling: A Definitive Guide for Metal Fabricators
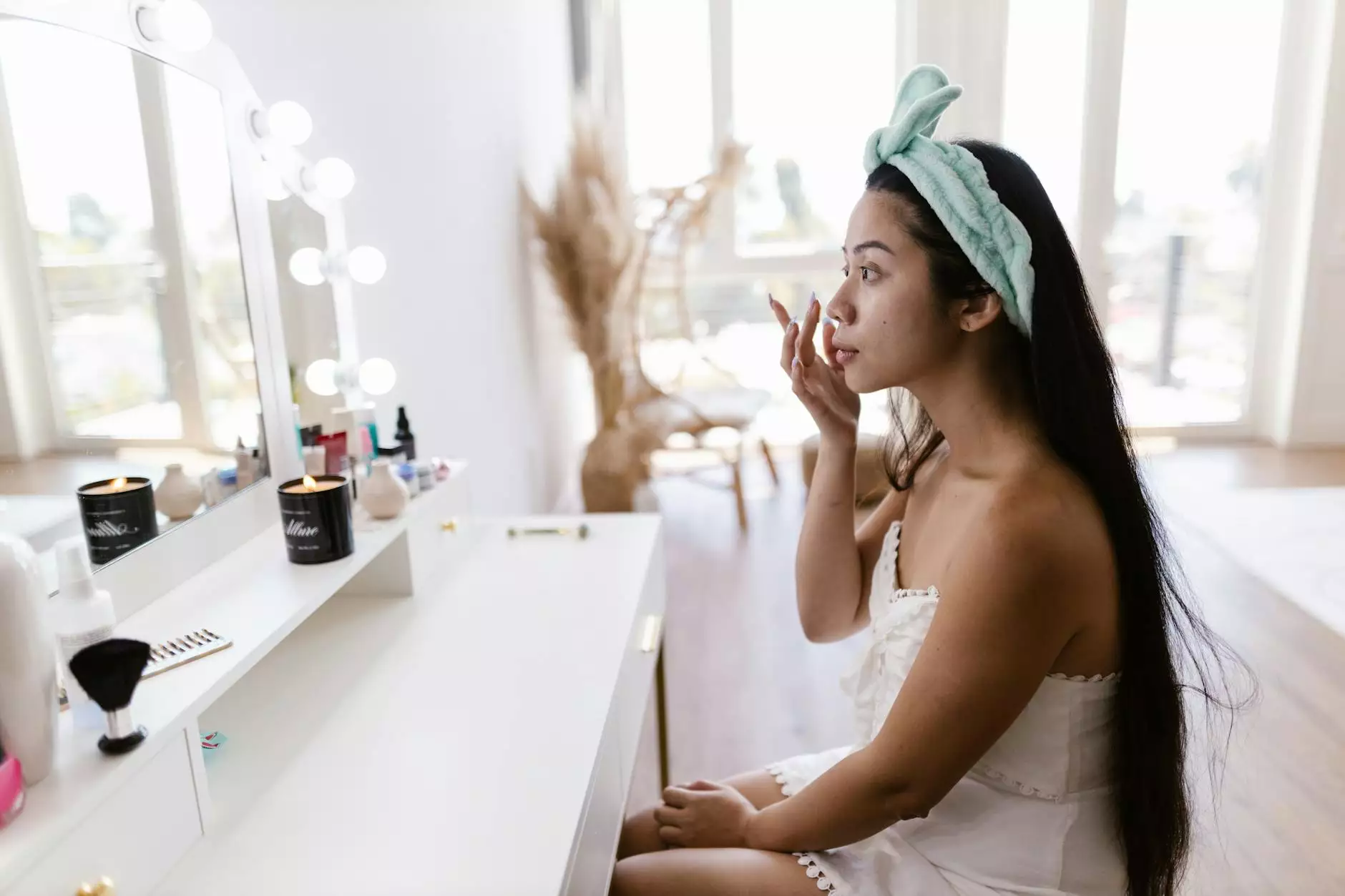
The manufacturing industry is undergoing rapid transformation, driving the need for innovative solutions that enhance efficiency, reduce costs, and improve product quality. One such method that has gained immense popularity is high pressure die casting tooling. This article delves deeply into what high pressure die casting is, its tooling aspects, applications, and why it's essential for metal fabricators.
What is High Pressure Die Casting?
High pressure die casting is a manufacturing process in which molten metal is forced into a mold cavity under high pressure. This technique is typically used for non-ferrous metals, such as aluminum, zinc, and magnesium. The process allows for the creation of complex shapes and intricate designs with excellent dimensional accuracy and surface finish.
The Process of High Pressure Die Casting
The process of high pressure die casting can be broken down into distinct stages:
- Metal Melting: The metal is heated until it reaches a liquid state, typically in a furnace designed specifically for this purpose.
- Injection: The molten metal is injected into the die at high pressure, ensuring it fills all cavities effectively.
- Solidification: Once the metal is in the mold, it begins to cool and solidify.
- Die Opening: After cooling for a predetermined time, the die is opened to release the finished part.
- Finishing: The part is then removed and may undergo secondary processes like machining or surface treatment.
Importance of Tooling in High Pressure Die Casting
The role of high pressure die casting tooling is crucial in determining the overall quality and efficiency of the die casting process. Tooling refers to the design and manufacturing of the molds used in die casting. High-quality tooling can dramatically affect production rates, part quality, and operational costs.
Characteristics of Effective Die Casting Tooling
- Durability: Tooling must withstand the high pressures and temperatures associated with the die casting process.
- Precision: Accurate design ensures that the final product meets the required specifications, reducing waste and rework.
- Heat Conductivity: Efficient heat dissipation during the casting process minimizes cycle times and improves surface finishes.
Types of High Pressure Die Casting Tooling
There are primarily two types of tooling used in high pressure die casting:
- Single Cavity Tooling: This type produces one part per cycle, which is ideal for limited production runs.
- Multi-Cavity Tooling: Designed to produce multiple parts simultaneously, this tooling is effective for mass production, significantly reducing cycle times and costs.
Applications of High Pressure Die Casting
High pressure die casting is used in various industries due to its efficiency and versatility:
Automotive Industry
In the automotive sector, components such as engine blocks, transmission cases, and structural parts are manufactured using high pressure die casting tooling. This method provides high-strength parts that contribute to the overall vehicle performance and safety.
Aerospace Industry
The aerospace industry leverages high pressure die casting for lightweight yet durable components, essential for fuel efficiency and performance. Components like brackets, housings, and fittings are commonly produced.
Electronics Industry
High pressure die casting tooling also plays a vital role in the electronics sector, where heat sinks, enclosures, and complex internal components are produced with precision and reliability.
Benefits of Using High Pressure Die Casting Tooling
The adoption of high pressure die casting tooling offers numerous advantages:
- High Production Efficiency: The speed of the die casting process allows for rapid production cycles, particularly in mass production scenarios.
- Excellent Dimensional Accuracy: High pressure injection ensures that the metal fills every detail of the mold, resulting in parts that require minimal machining.
- Reduced Waste: The precision of the casting process minimizes excess material, making it a cost-effective solution.
- Complex Geometries: The ability to create intricate shapes that are difficult or impossible to machine from solid blocks of metal.
Challenges in High Pressure Die Casting Tooling
While the benefits are significant, there are also challenges that manufacturers may face:
Design and Manufacturing Costs
High-quality tooling can require substantial upfront investment. However, this is often offset by the long-term savings in production costs and reduced waste.
Tooling Life and Maintenance
Maintaining the tooling to ensure longevity is crucial. Regular inspections and maintenance can help identify wear and prevent costly downtime.
Conclusion: The Future of High Pressure Die Casting Tooling
The demand for high pressure die casting tooling continues to grow as industries seek more efficient and cost-effective manufacturing solutions. With advancements in technology, including automation and computer-aided design, manufacturers can expect even greater precision and efficiency in creating high-quality components.
As a metal fabricator, investing in high pressure die casting tooling represents not just an improvement to your manufacturing process, but a commitment to quality and excellence in today's competitive market. Companies like DeepMould.net are at the forefront of this innovation, offering expertise and dedication that can help your business thrive in the evolving landscape of manufacturing.
By embracing high pressure die casting and leveraging its extensive benefits, you can stay ahead of the curve, delivering superior products that meet customer demands and regulatory standards.